Advantages of using SMT Solder-Down System-on-Modules
System on Modules (SOMs) are a great way to build core computing components such as processors, memory, and I/O into a device – with SOMs, integrators can save money and reduce design complexity. Soldered SOMs is an evolution that builds on the existing benefits of SOMs. In this article, we explain what a solder-down SOM is, how it differs physically from a traditional module, and explain what benefits solder-down SOMs bring to integrators.
What is a solder-down SOM?
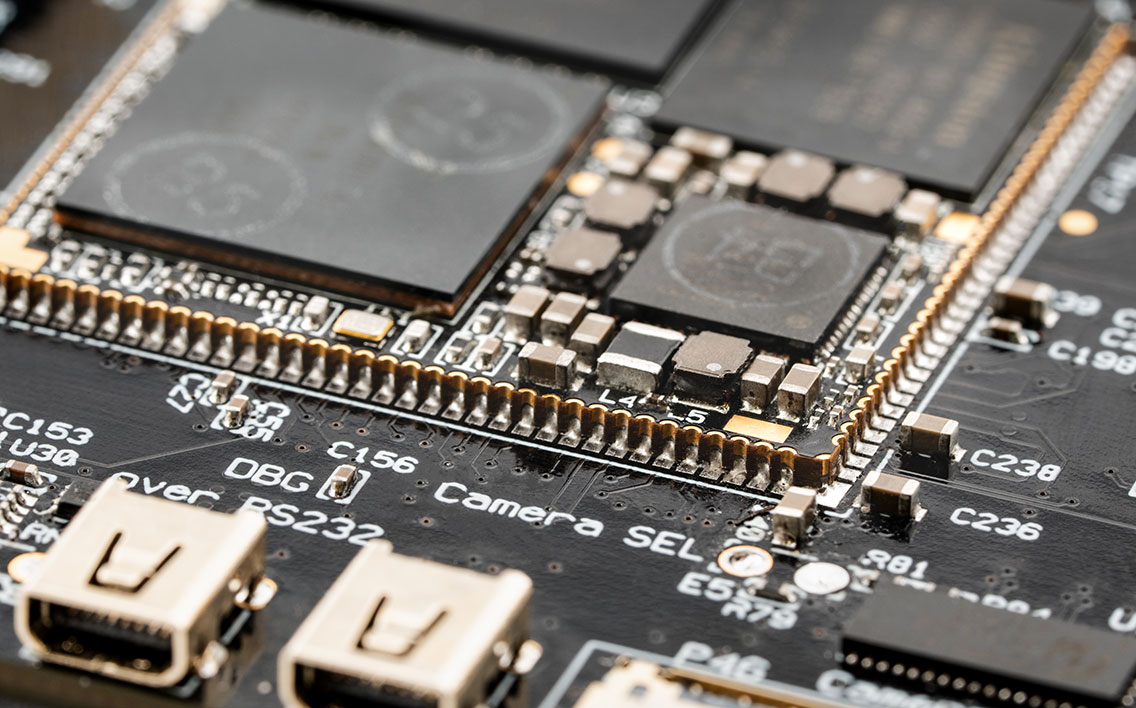
A solder-down System-on-Module (SOM) offers a miniature, self-contained computer system that’s permanently integrated into a custom-designed carrier board. Unlike SOMs that rely on connectors for attachment to the board, solder-down SOMs are surface-mount components, soldered directly onto the carrier board.
Because the SOM is soldered to the board there is a complete absence of connectors. It means that a solder-down SOM has a remarkably reduced height profile – and that solder-down SOMs take up less space.
The direct soldered connection between the SOM and carrier board also establishes a robust mechanical bond – more stable than a traditional connector, and more resistant to vibration and shocks. A soldered connection also arguably contributes to improved signal integrity by minimizing signal loss and crosstalk, ultimately enhancing overall system performance.
The advantages of using a solder-down SOM
For many use cases, standard SOMs that rely on physical sockets to attach to a board are fine. But solder-down SOMs have plenty to offer in the right circumstances. One of the main advantages is simple: solder-down SOMs reduce manual steps because there are no boards to plug in. Other integration benefits include:
- Reduced Height Profile – by eliminating connectors, solder-down SOMs offer a significantly reduced height profile. In some devices, space is at an extreme premium: think about wearables, for example. Eliminating the socket and using a solder-down SOM can make all the difference.
- Enhanced Robustness – a soldered connection is simply a much stronger and more reliable mechanical bond between the SOM and the carrier board. Again, this matters more in some environments than in others – but industrial and rugged applications where shock and vibration is a factor are clear use cases for solder-down SOMs, which are less affected by vibration.
- Improved Signal Integrity – direct soldering minimizes signal loss and crosstalk, resulting in improved overall signal integrity and system performance. It helps maintain signal integrity and compliance with electromagnetic compatibility (EMC) standards.
- Simplified Manufacturing – integrating solder-down SOMs streamlines manufacturing and reduces production costs. There are no connectors, so solder-down SoMs reduce the bill of materials (BOM) cost. The absence of connectors also simplifies the overall design, with fewer points of mechanical failure.
- Thermal Efficiency – the way solder-down SoMs couple to the component board often aids in heat dissipation. This design helps in efficiently transferring heat to the baseboard, reducing the need for additional cooling solutions like heatsinks. It is particularly beneficial in high-performance applications where thermal management is critical.
Benefits of solder-down SOMs from Compulab
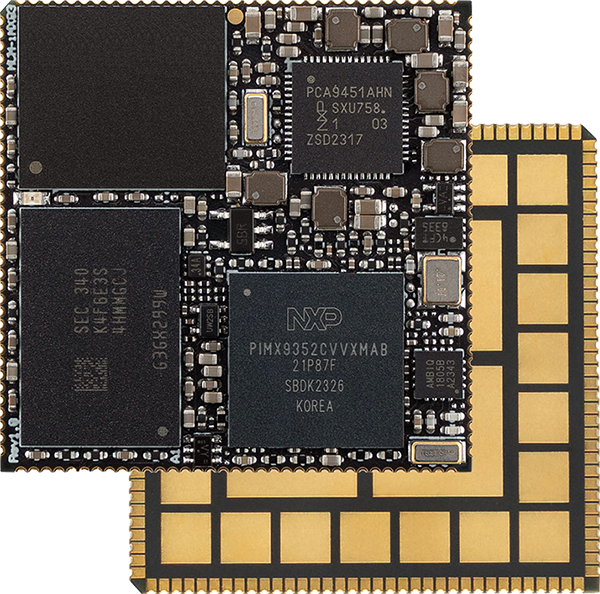
Compulab’s MCM-iMX93 captures all the advantages of solder-down SOMs. With the powerful NXP i.MX9352 processor, you get ample memory, and a rich array of interfaces, all integrated into an ultra-compact form factor.
The MCM-iMX93’s low profile delivers exceptional performance while consuming minimal space. It is perfect for space-constrained applications such as wearables, handheld devices, and miniature IoT sensors.
A robust mechanical connection means the MCM-iMX93 is well-suited for transportation, agriculture, defense, and aerospace applications that require tolerance against high temperatures and vibration. It also supports a simplified and cost-efficient manufacturing process, ideal for high-volume production scenarios.
Whether it’s designing compact wearables, rugged industrial controllers, or cost-effective IoT sensors, Compulab’s solder-down SOMs provide a versatile and reliable foundation for a wide spectrum of embedded applications.
Conclusions
Solder-down SOMs are an advancement that has big advantages for certain use cases. Compulab’s MCM-iMX93 delivers all these benefits in an affordable module. With the MCM-iMX93 you get a rugged, shock and vibration-resistant SOM that uses the minimum footprint – ideal for the toughest, most space-constrained environments.
Visit the MCM-iMX93 product page to find out more about the Compulab solder-down SOM – complete development resources, a link to an evaluation kit, and how to order.